- Bina Rumah Batu-Bata
- Zero Deposit
- Spesifikasi Rumah
- Lokasi Projek
- Pembiayaan LPPSA
- Garis Panduan LPPSA (Rasmi)
- Soalan Lazim LPPSA
- E-Book LPPSA (Download)
- 1. Apa itu LPPSA?
- 2. Kelebihan LPPSA
- 3. Syarat Kelayakan
- 4. Jenis-Jenis Pembiayaan
- Jenis 1 – Pembelian Rumah Kediaman Yang Telah Siap
- Jenis 2 – Membina Rumah Di Atas Tanah Sendiri
- Jenis 3 – Membeli Rumah Kediaman Yang Sedang Dibina
- Jenis 4 – Pembelian Tanah Bagi Pembinaan Rumah
- Jenis 5 – Melunaskan Keseluruhan/ Sebahagian Pinjaman Sedia Ada Daripada Bank/ Institusi Kewangan
- Jenis 6 – Pembinaan Rumah Kediaman Di Atas Tanah Yang Sedang Dibiayai Oleh BPP/ LPPSA
- Jenis 7 – Ubah Suai Rumah Yang Sedang Atau Telah Selesai Bayar Melalui LPPSA
- 5. Semak Kelayakan LPPSA
- 6. Dokumen Yang Diperlukan
- 7. Insurans/ Takaful LPPSA
- 8. Kos Yuran Guaman
- 9. BONUS: Bina Rumah
- Pembiayaan Koperasi
- Pengeluaran KWSP
- Bayaran Tunai
- Kalkulator
Analyzing IBS Construction Costs in Malaysia: A Comprehensive Guide
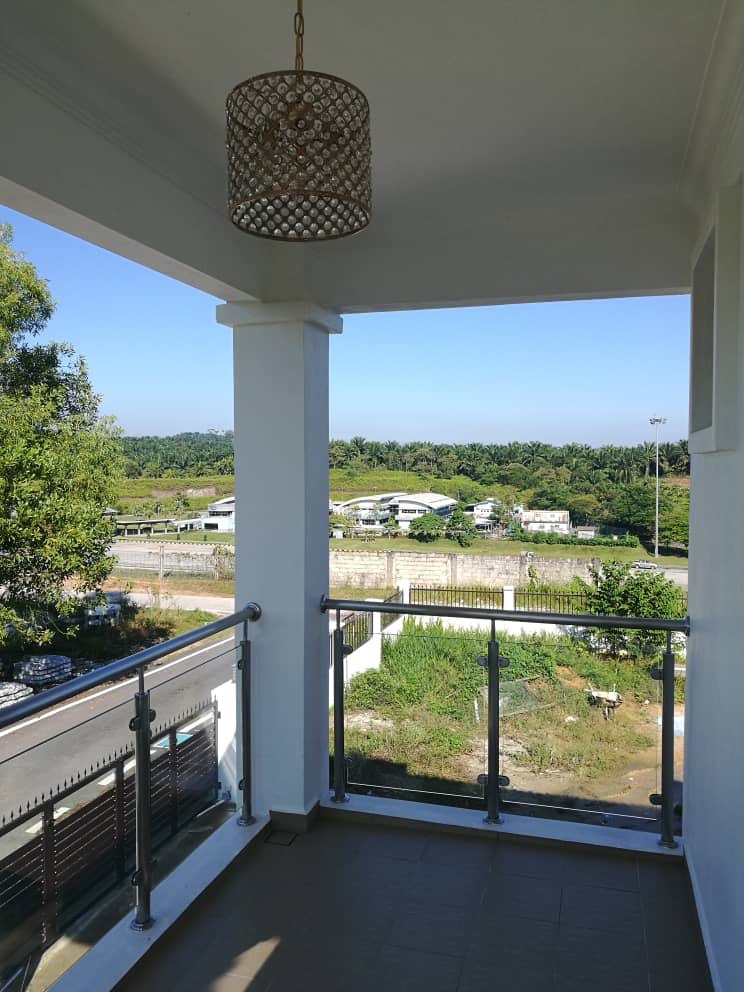
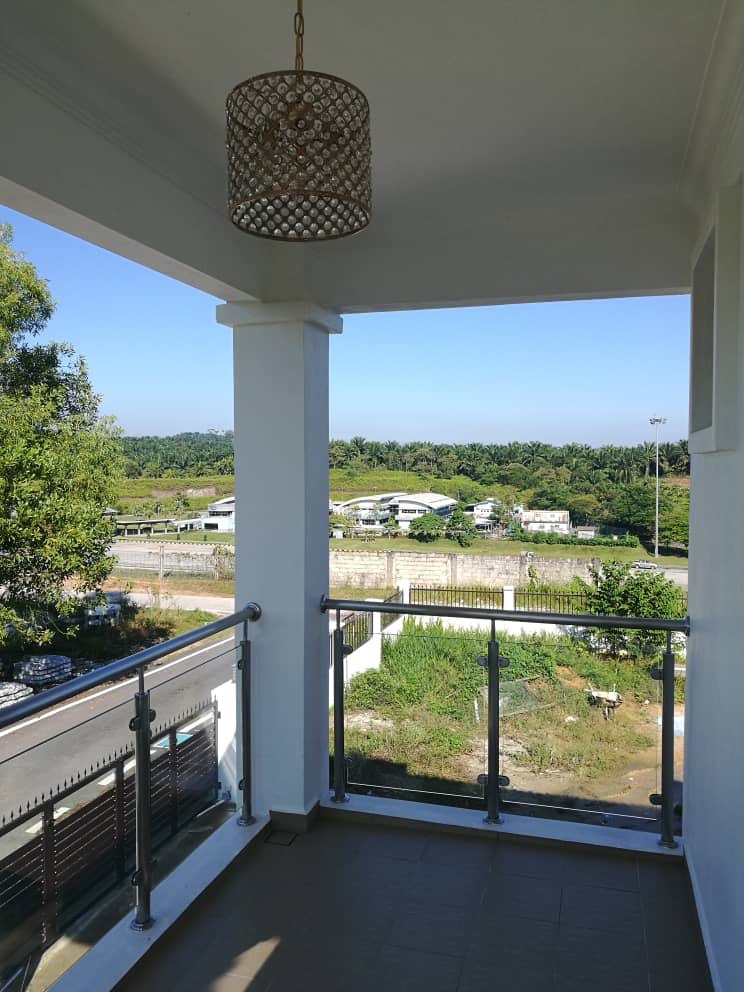
Analyzing IBS Construction Costs in Malaysia: A Comprehensive Guide
Introduction
In recent years, the construction industry in Malaysia has undergone a significant transformation with the increasing adoption of Industrialized Building System (IBS) construction. IBS has emerged as a game-changer, revolutionizing the way buildings are constructed. This article aims to provide a comprehensive analysis of IBS construction costs in Malaysia. By understanding the factors that influence expenses, stakeholders can make informed decisions, optimize project budgets, and achieve cost-effective and sustainable building solutions.
Understanding Industrialized Building System (IBS)
Industrialized Building System (IBS) is a construction method that involves the manufacturing of building components off-site, followed by their assembly on-site. The utilization of pre-fabricated components and modular systems enhances productivity, quality, and sustainability in construction projects. IBS methods can range from panel systems to volumetric modules, each offering unique benefits and cost implications.
Advantages of Implementing IBS in Construction Projects
Implementing IBS in construction projects offers numerous advantages compared to traditional construction methods. Let’s explore some of these key advantages:
- Enhanced Productivity: IBS construction reduces labor-intensive tasks, streamlines construction processes, and improves project timelines, resulting in faster project completion.
- Reduced Construction Waste: By optimizing material usage and minimizing on-site construction activities, IBS significantly reduces construction waste, making it an environmentally friendly choice.
- Improved Quality and Structural Integrity: IBS components are manufactured with precision and can be engineered to meet specific requirements, ensuring higher quality, durability, and structural integrity of the buildings.
- Increased Cost Savings: While initial investments in IBS machinery and equipment might seem significant, IBS construction projects often yield long-term cost savings due to reduced labor requirements and shorter project durations.
Factors Influencing IBS Construction Costs
Several factors influence the costs associated with IBS construction projects. Understanding these factors is crucial for accurate cost estimation and effective project management. Let’s delve into the key factors that impact IBS construction costs:
1. Design Complexity
The complexity of the building design directly impacts the costs of IBS construction. Intricate designs may require customized prefabricated components, which can increase manufacturing and assembly expenses. Careful consideration and collaboration between architects, engineers, and manufacturers are essential to strike a balance between design complexity and cost-efficiency.
2. Project Scale
The scale of the project plays a significant role in determining IBS construction costs. Larger projects may benefit from economies of scale, leading to potential cost savings. On the other hand, smaller-scale projects may face higher unit costs due to the setup and operational costs associated with IBS production facilities.
3. Site Conditions
Site conditions can significantly impact IBS construction costs. Factors such as limited access, uneven terrain, or difficult logistics can increase transportation and installation expenses. Conducting a thorough site analysis and planning for potential challenges will help mitigate these additional costs.
4. Material Selection
The choice of materials in IBS construction has a dual impact on both quality and costs. While opting for high-quality, durable materials might increase upfront costs, it can lead to long-term savings in maintenance and repair. It is crucial to strike the right balance between cost and quality, considering the specific requirements of each project.
5. Manufacturing and Assembly Processes
Efficient manufacturing and assembly processes play a crucial role in managing IBS construction costs. Well-organized production methods, streamlined assembly sequences, and effective supply chain management can reduce labor and time expenses. Adopting lean manufacturing principles and leveraging automation technologies can further enhance cost-effectiveness.
Initial Investment in IBS Machinery and Equipment
Embracing IBS construction projects requires an initial investment in specialized machinery and equipment. This includes setting up factories for component manufacturing, establishing automated production lines, and implementing transportation systems. While the upfront investment may seem substantial, it is essential to consider the long-term benefits and cost savings that IBS can offer.
Cost Savings in Labor and Time
One of the most significant advantages of IBS construction is the potential for cost savings in labor and time. With pre-fabricated components, construction activities on-site can be streamlined, leading to reduced labor requirements and shorter project durations. This can result in lower overall costs and improved project profitability. Additionally, reduced labor-intensive tasks translate to a safer work environment, mitigating the risk of accidents and injuries.
Material Costs in IBS Construction
Material costs account for a significant portion of IBS construction expenses. They encompass various elements, including the cost of raw materials, transportation, and storage. The choice of materials, such as concrete, steel, or timber, can significantly influence the overall expenses. It is crucial to strike a balance between material costs and quality considerations to ensure optimal project outcomes.
Maintenance and Repair Expenses
While IBS construction is known for its durability and quality, maintenance and repair costs should still be factored into the overall project budget. Regular inspections and necessary repairs over the lifespan of the building should be accounted for to maintain its integrity and functionality. Implementing proper maintenance protocols and leveraging predictive maintenance technologies can help optimize long-term maintenance costs.
Case Studies on IBS Construction Costs
Analyzing real-life case studies provides valuable insights into the costs associated with IBS construction. By examining various projects of different scales and complexities, it is possible to gain a comprehensive understanding of cost implications and identify areas for cost optimization. Studying successful IBS construction projects can inspire innovative approaches and highlight best practices for cost-effective implementation.
Challenges and Limitations of IBS Construction
Despite its advantages, IBS construction also faces challenges and limitations that need to be considered. These include the need for skilled labor, limited design flexibility compared to conventional construction methods, higher upfront investments, and potential compatibility issues between different IBS components. Recognizing and addressing these challenges through proper planning, training, and collaboration is crucial for successful project implementation and effective cost management.
Future Trends and Opportunities in IBS Construction
The future of IBS construction in Malaysia holds significant promise. Ongoing advancements in technology, such as Building Information Modeling (BIM), prefabrication automation, and robotics, are expected to make IBS methods even more efficient, cost-effective, and sustainable. As the industry evolves, opportunities for innovation and collaboration will arise, driving further improvements in IBS construction costs and expanding its applications across various construction sectors.
Conclusion
Analyzing IBS construction costs in Malaysia reveals the intricate factors that contribute to overall expenses. From design complexity to material selection, manufacturing processes, and site conditions, each aspect plays a crucial role in determining the cost implications of IBS construction projects. While the initial investment in machinery and equipment may seem substantial, the long-term cost savings in labor, time, and maintenance justify the adoption of IBS methods. By carefully considering these factors and leveraging the advantages of IBS construction, stakeholders can achieve cost-effective, sustainable, and high-quality building solutions.
FAQs
- What is IBS construction? IBS construction refers to a method that involves the use of pre-fabricated components and modular systems, aiming to improve productivity, quality, and sustainability in the construction process.
- How does IBS construction save costs? IBS construction saves costs through reduced labor requirements, shorter project durations, and optimized material usage.
- Are there any limitations to IBS construction? Yes, some limitations of IBS construction include the need for skilled labor, limited design flexibility, and higher upfront investments.
- What are the advantages of IBS construction? The advantages of IBS construction include enhanced productivity, reduced construction waste, improved quality, and structural integrity.
-
What does the future hold for IBS construction in Malaysia? The future of IBS construction in Malaysia looks promising, with ongoing advancements in technology and opportunities for innovation driving further improvements in cost-effectiveness and sustainability.