- Bina Rumah Batu-Bata
- Zero Deposit
- Spesifikasi Rumah
- Lokasi Projek
- Pembiayaan LPPSA
- Garis Panduan LPPSA (Rasmi)
- Soalan Lazim LPPSA
- E-Book LPPSA (Download)
- 1. Apa itu LPPSA?
- 2. Kelebihan LPPSA
- 3. Syarat Kelayakan
- 4. Jenis-Jenis Pembiayaan
- Jenis 1 – Pembelian Rumah Kediaman Yang Telah Siap
- Jenis 2 – Membina Rumah Di Atas Tanah Sendiri
- Jenis 3 – Membeli Rumah Kediaman Yang Sedang Dibina
- Jenis 4 – Pembelian Tanah Bagi Pembinaan Rumah
- Jenis 5 – Melunaskan Keseluruhan/ Sebahagian Pinjaman Sedia Ada Daripada Bank/ Institusi Kewangan
- Jenis 6 – Pembinaan Rumah Kediaman Di Atas Tanah Yang Sedang Dibiayai Oleh BPP/ LPPSA
- Jenis 7 – Ubah Suai Rumah Yang Sedang Atau Telah Selesai Bayar Melalui LPPSA
- 5. Semak Kelayakan LPPSA
- 6. Dokumen Yang Diperlukan
- 7. Insurans/ Takaful LPPSA
- 8. Kos Yuran Guaman
- 9. BONUS: Bina Rumah
- Pembiayaan Koperasi
- Pengeluaran KWSP
- Bayaran Tunai
- Kalkulator
Calculating the Cost-Benefit Ratio of IBS Construction
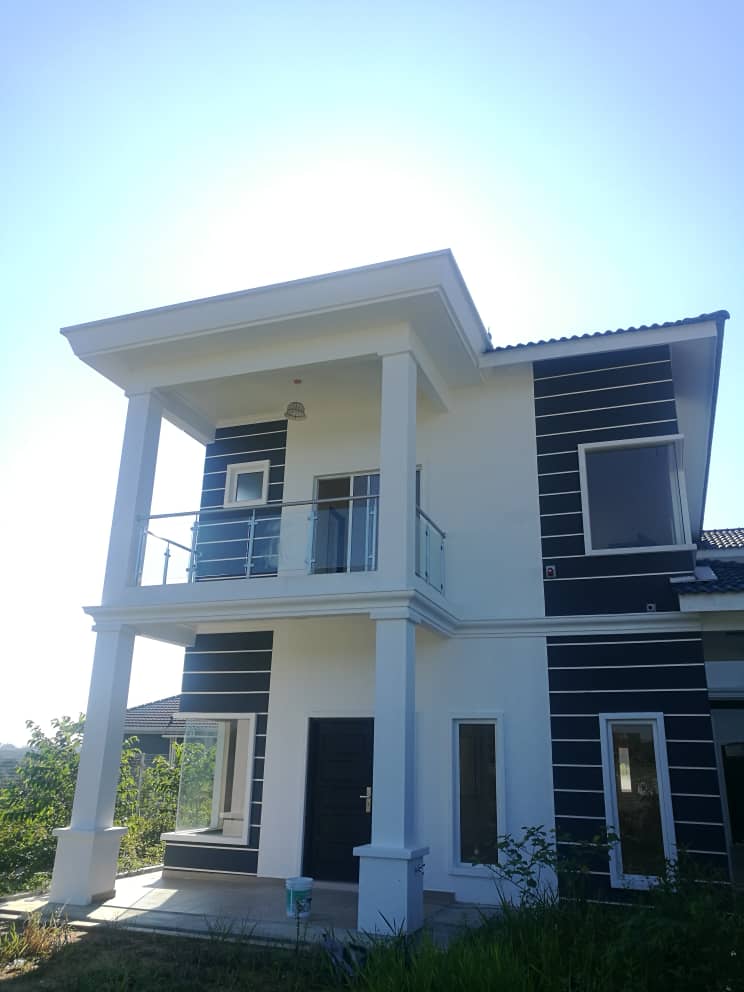
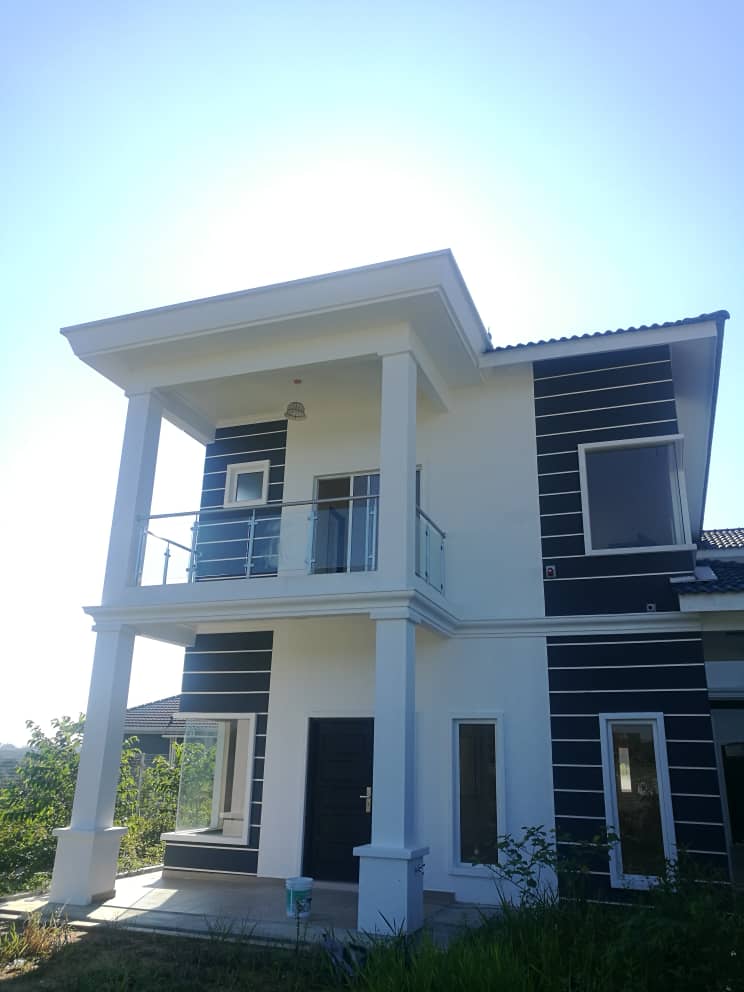
Calculating the Cost-Benefit Ratio of IBS Construction
Introduction:
In the construction industry, the adoption of modern construction methods is gaining momentum. One such method is Industrialized Building System (IBS) construction. IBS involves the use of pre-fabricated components that are manufactured off-site and then assembled on-site. This article aims to explore the cost-benefit ratio of IBS construction and its implications for the industry.
Table of Contents
- What is IBS Construction?
- Advantages of IBS Construction 2.1 Speed and Efficiency 2.2 Cost Savings 2.3 Quality and Consistency 2.4 Environmental Sustainability
- Cost Factors in IBS Construction 3.1 Initial Investment 3.2 Transportation and Logistics 3.3 Training and Skills 3.4 Maintenance and Operational Costs
- Calculating the Cost-Benefit Ratio
- Case Studies
- Challenges and Limitations
- Future Prospects of IBS Construction
- Conclusion
- FAQs
1. What is IBS Construction?
IBS construction refers to the method of constructing buildings using pre-fabricated components that are manufactured in a controlled environment off-site. These components include wall panels, floor slabs, columns, beams, and other structural elements. The pre-fabricated components are then transported to the construction site for assembly. IBS offers several advantages over traditional construction methods, making it an attractive option for developers and contractors.
2. Advantages of IBS Construction
2.1 Speed and Efficiency
Using pre-fabricated components speeds up the construction process. As the components are manufactured off-site, construction activities on-site can proceed simultaneously, reducing the overall construction time. This leads to faster project completion, allowing developers to save time and money.
2.2 Cost Savings
IBS construction can result in significant cost savings. The controlled manufacturing environment reduces material wastage and enhances efficiency. Additionally, the reduced construction time translates into lower labor costs. Overall, IBS construction offers a cost-effective solution for both residential and commercial projects.
2.3 Quality and Consistency
The controlled manufacturing environment of IBS ensures consistent quality in the pre-fabricated components. The use of standardized processes and materials leads to higher precision and accuracy, resulting in structurally sound buildings. The quality control measures minimize defects and enhance the durability of the construction.
2.4 Environmental Sustainability
IBS construction is considered more environmentally friendly compared to traditional construction methods. The use of pre-fabricated components reduces construction waste and minimizes the impact on the environment. Additionally, IBS allows for the integration of sustainable features such as energy-efficient systems and renewable materials.
3. Cost Factors in IBS Construction
3.1 Initial Investment
The initial investment in IBS construction might be higher compared to traditional methods due to the need for specialized equipment and facilities. However, this cost can be offset by the long-term benefits of reduced construction time and lower operational expenses.
3.2 Transportation and Logistics
Transportation costs play a significant role in IBS construction. The transportation of pre-fabricated components from the manufacturing facility to the construction site should be carefully planned to minimize costs. Efficient logistics management ensures timely delivery and reduces the risk of delays.
3.3 Training and Skills
IBS construction requires skilled workers who are familiar with the assembly of pre-fabricated components. Training costs and the availability of skilled labor should be considered when evaluating the cost-benefit ratio. Proper training programs can enhance productivity and reduce the risk of errors during assembly.
3.4 Maintenance and Operational Costs
While IBS construction offers cost savings during the initial construction phase, it is essential to consider maintenance and operational costs in the long run. Proper maintenance and regular inspections are necessary to ensure the longevity of the IBS components and the overall building structure.
4. Calculating the Cost-Benefit Ratio
To calculate the cost-benefit ratio of IBS construction, a comprehensive analysis of the costs and benefits is necessary. The following steps can be followed:
- Identify all relevant cost factors, including initial investment, transportation costs, training expenses, and maintenance/operational costs.
- Assign a monetary value to each cost factor.
- Determine the expected benefits, such as reduced construction time, lower labor costs, improved quality, and long-term savings.
- Assign a monetary value to each benefit.
- Calculate the net present value (NPV) by subtracting the total costs from the total benefits.
- Divide the NPV by the initial investment to obtain the cost-benefit ratio.
The cost-benefit ratio provides a quantitative measure of the financial viability of implementing IBS construction methods.
5. Case Studies
Case studies play a crucial role in evaluating the cost-benefit ratio of IBS construction. By analyzing real-world projects, the industry can gain valuable insights into the potential benefits and challenges. Case studies should consider factors such as project size, location, timeline, and cost savings achieved through IBS construction. These studies provide practical examples that developers and contractors can refer to when considering the adoption of IBS construction methods.
6. Challenges and Limitations
While IBS construction offers numerous advantages, it also faces certain challenges and limitations. These include:
- Limited design flexibility compared to traditional construction methods.
- High initial investment costs, especially for small-scale projects.
- The need for skilled labor and specialized training programs.
- Transportation and logistics complexities, especially for large-scale projects in remote areas.
Understanding and addressing these challenges is crucial for successful implementation and maximizing the cost-benefit ratio of IBS construction.
7. Future Prospects of IBS Construction
The future prospects of IBS construction are promising. As the construction industry continues to embrace sustainable and efficient practices, the demand for IBS is expected to increase. Technological advancements, such as Building Information Modeling (BIM) and automation, further enhance the feasibility and cost-effectiveness of IBS construction. With ongoing research and development, IBS methods are likely to evolve and offer even greater benefits in the future.
8. Conclusion
In conclusion, IBS construction presents a cost-effective and sustainable solution for the construction industry. By calculating the cost-benefit ratio, developers and contractors can evaluate the financial viability of implementing IBS methods. The advantages of speed, cost savings, quality, and sustainability make IBS an attractive option. However, it is crucial to consider the specific cost factors and challenges associated with IBS construction to make informed decisions.
9. FAQs
Q1: Is IBS construction suitable for all types of projects? A1: IBS construction can be applied to various projects, including residential, commercial, and industrial buildings. However, the suitability depends on project requirements and factors such as size, location, and design flexibility.
Q2: How does IBS construction contribute to sustainability? A2: IBS construction reduces material wastage, minimizes the environmental impact, and allows for the integration of energy-efficient systems and renewable materials.
Q3: What are the training requirements for IBS construction? A3: Skilled workers are required for the assembly of pre-fabricated components. Training programs focusing on IBS construction techniques and safety protocols are essential to ensure the successful implementation of IBS methods.
Q4: Can IBS construction reduce construction time? A4: Yes, IBS construction significantly reduces construction time by allowing for simultaneous off-site manufacturing and on-site assembly of pre-fabricated components.
Q5: Are there any government initiatives to promote IBS construction? A5: Many countries have introduced incentives and initiatives to encourage the adoption of IBS construction. These initiatives aim to improve productivity, quality, and sustainability in the construction industry.