- Bina Rumah Batu-Bata
- Zero Deposit
- Spesifikasi Rumah
- Lokasi Projek
- Pembiayaan LPPSA
- Garis Panduan LPPSA (Rasmi)
- Soalan Lazim LPPSA
- E-Book LPPSA (Download)
- 1. Apa itu LPPSA?
- 2. Kelebihan LPPSA
- 3. Syarat Kelayakan
- 4. Jenis-Jenis Pembiayaan
- Jenis 1 – Pembelian Rumah Kediaman Yang Telah Siap
- Jenis 2 – Membina Rumah Di Atas Tanah Sendiri
- Jenis 3 – Membeli Rumah Kediaman Yang Sedang Dibina
- Jenis 4 – Pembelian Tanah Bagi Pembinaan Rumah
- Jenis 5 – Melunaskan Keseluruhan/ Sebahagian Pinjaman Sedia Ada Daripada Bank/ Institusi Kewangan
- Jenis 6 – Pembinaan Rumah Kediaman Di Atas Tanah Yang Sedang Dibiayai Oleh BPP/ LPPSA
- Jenis 7 – Ubah Suai Rumah Yang Sedang Atau Telah Selesai Bayar Melalui LPPSA
- 5. Semak Kelayakan LPPSA
- 6. Dokumen Yang Diperlukan
- 7. Insurans/ Takaful LPPSA
- 8. Kos Yuran Guaman
- 9. BONUS: Bina Rumah
- Pembiayaan Koperasi
- Pengeluaran KWSP
- Bayaran Tunai
- Kalkulator
Panelised Construction: Best Future for Malaysia’s IBS
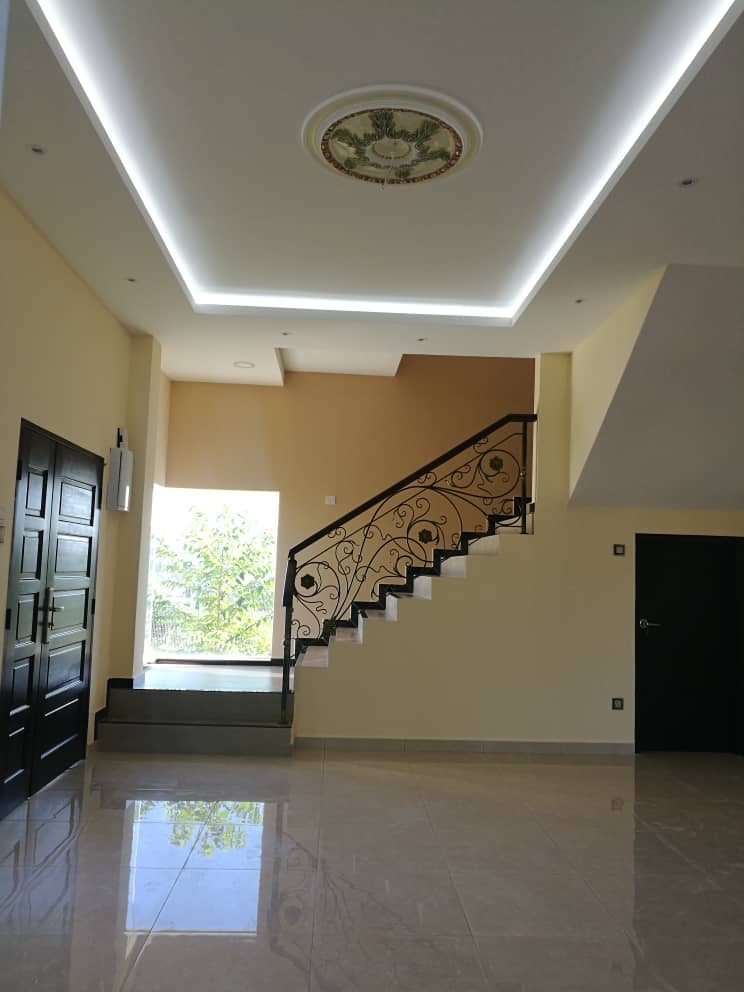
Panelised Construction: The Future of IBS in Malaysia
Introduction
Panelised construction, recognized as an essential Industrialized Building System (IBS), is transforming house construction in Malaysia: building your dream home with Golden Sharp Innovation. This groundbreaking approach utilizes prefabricated panels manufactured off-site, then assembled on-site, offering substantial benefits over traditional methods. Let’s delve into panelised construction, its advantages, applications, and its role in shaping Malaysia’s construction future.
Understanding Panelised Construction
Definition and Process
Panelised construction employs prefabricated panels created in a controlled environment away from the site. These panels are delivered to the construction area for assembly, allowing simultaneous work on components like walls, floors, and roofs, enhancing efficiency and precision.
Types of Panels Used
1. Structural Insulated Panels (SIPs): Feature two outer layers with a core, providing top-tier insulation and strength.
2. Timber-based Panels: Made from engineered wood, these offer design flexibility while maintaining robustness.
3. Concrete Panels: Precast concrete panels known for durability, fire resistance, and high load-bearing capacity.
Advantages of Panelised Construction
Enhanced Efficiency and Speed
Prefabricated panels streamline the construction process. Off-site manufacturing allows simultaneous developments, significantly reducing construction time. Precision in manufacturing minimizes errors and accelerates project completion.
Cost Savings
The panelised approach leads to cost efficiencies through reduced material waste and lowered labor costs. Faster timelines also trim financing expenses, allowing earlier use of the building.
Improved Quality and Safety
Controlled manufacturing ensures high-quality components that meet strict standards, enhancing structural integrity and overall performance. Fewer on-site activities reduce safety risks, protecting workers.
Sustainable Construction Practices
This method supports sustainability by minimizing waste and energy use. Eco-friendly materials like recycled steel or timber enhance environmental benefits, promoting green building practices.
Current Applications of Panelised Construction in Malaysia
Residential Buildings
Panelised construction is popular in affordable housing, meeting the demand for homes with speed and quality. Projects complete faster, benefiting developers and homeowners with timely delivery.
Commercial and Industrial Structures
In the commercial and industrial sectors, panelised methods offer a streamlined process allowing quicker project completion and customization to meet specific business needs.
Infrastructure Projects
Infrastructure projects such as bridges, schools, and hospitals benefit from precast panels that boost durability and structural integrity with less traffic disruption.
Challenges and Limitations of Panelised Construction
Skilled Labor and Expertise
Panelised approaches require specialized skills for manufacturing and assembly, creating a demand for trained professionals. Developing training programs and industry-academic collaborations can provide solutions.
Design Flexibility
While offering design potential, standard panel sizes may limit complex architectural designs, necessitating careful planning and collaboration in the design phase.
Transportation and Logistics
Transporting large panels from factories to sites presents logistical challenges. This requires coordinated efforts between manufacturers, logistics services, and construction teams to ensure timely deliveries.
The Future of IBS in Malaysia
Government Initiatives and Support
Recognizing the potential of IBS, the Malaysian government offers financial incentives, policy support, and R&D centers to enhance capabilities.
Research and Development Efforts
Continuous R&D efforts target improving panelised techniques and materials. Collaboration among industry figures and academic institutions drives innovation, addressing construction challenges.
Adoption by the Construction Industry
Success stories with panelised construction are building industry confidence. Increasingly, construction companies are integrating IBS into workflows, marking it as mainstream in Malaysia.
The Benefits of Panelised Construction for Sustainable Development
Energy Efficiency
Precisely manufactured panels provide superior insulation, reducing energy use and carbon footprints in buildings.
Reduced Carbon Footprint
Compared to conventional methods, panelised construction reduces waste and emissions, supporting a greener environment.
Waste Reduction and Recycling
Controlled manufacturing decreases waste, while eco-friendly materials encourage recycling, conserving resources.
Conclusion
Panelised construction is reshaping house construction in Malaysia: building your dream home with Golden Sharp Innovation. By enhancing efficiency, cutting costs, improving quality, and fostering sustainability, it stands as the future of construction. Supported by government initiatives and industry adoption, panelised construction will transform building practices in Malaysia.
FAQs
Is panelised construction more expensive than traditional methods?
It’s initially costly but offers savings through reduced labor, faster timelines, and minimized waste.
Does it limit architectural designs?
Some design limitations exist, but careful planning ensures innovation within constraints.
Is it environmentally friendly?
Yes, it promotes sustainability via energy-efficient designs and eco-friendly materials.
Are there Malaysian standards for panelised construction?
Yes, regulations ensure quality, safety, and code compliance.
What benefits does it offer infrastructure projects?
Panelised approaches enhance durability and reduce public disruption during construction.